latest
Innovative Horizons: Crafting new manufacturing design typologies
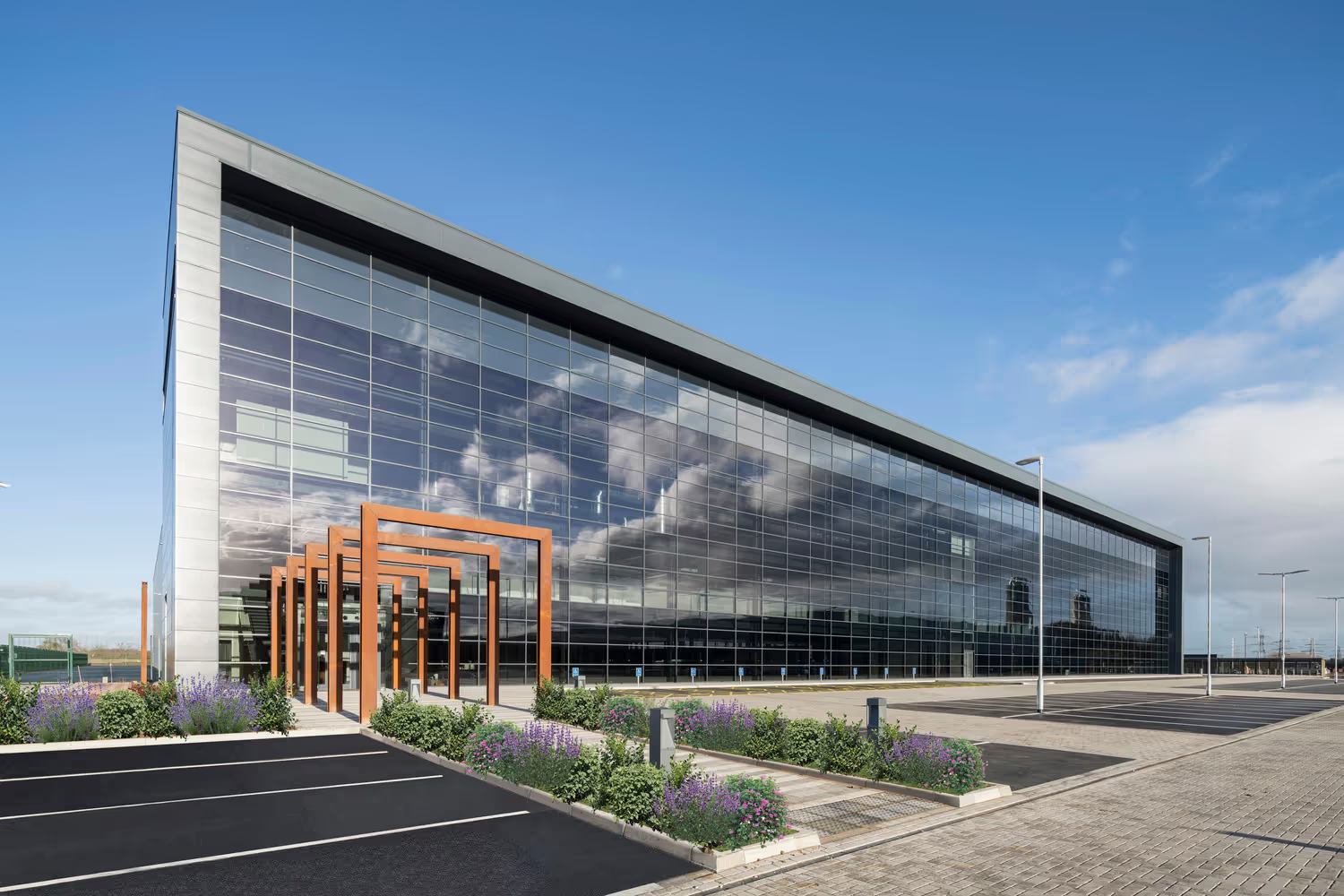
The design and delivery of industrial buildings increasingly requires an approach which can provide the most efficient and sustainable combination of different uses – such as workshops, manufacturing and production, assembly, storage, transportation and distribution – in one facility, while maximizing space, efficiency and flexibility for future growth and changes of use.
In addition, with a shrinking labour supply, many manufacturing and distribution developers and businesses are looking to optimise their sites to facilitate both more robots and also a more human-centric approach to attract and retain a workforce.
Industrial and logistics developments also need to incorporate the enhanced building and materials features that will deliver positive construction and in-use economic and environmental performance and impacts, ideally managed by state-of-the-art building environmental management and analytics systems.
Chetwoods industrial and logistics teams are currently designing a range of industrial and manufacturing projects that bring together all these requirements.
More efficient buildings and processes
We recently completed a 136,000 sqft manufacturing facility and distribution centre for leading UK composite door manufacturer Solidor which repurposed a brownfield site on the final plot at GLP’s G-Park Stoke development in Stoke-on-Trent. The project combined Solidor’s current production and storage facilities from five sites into a single hub, with a ‘best-in-class’ specification including 15 metres clear internal height, four dock doors and six level access doors.
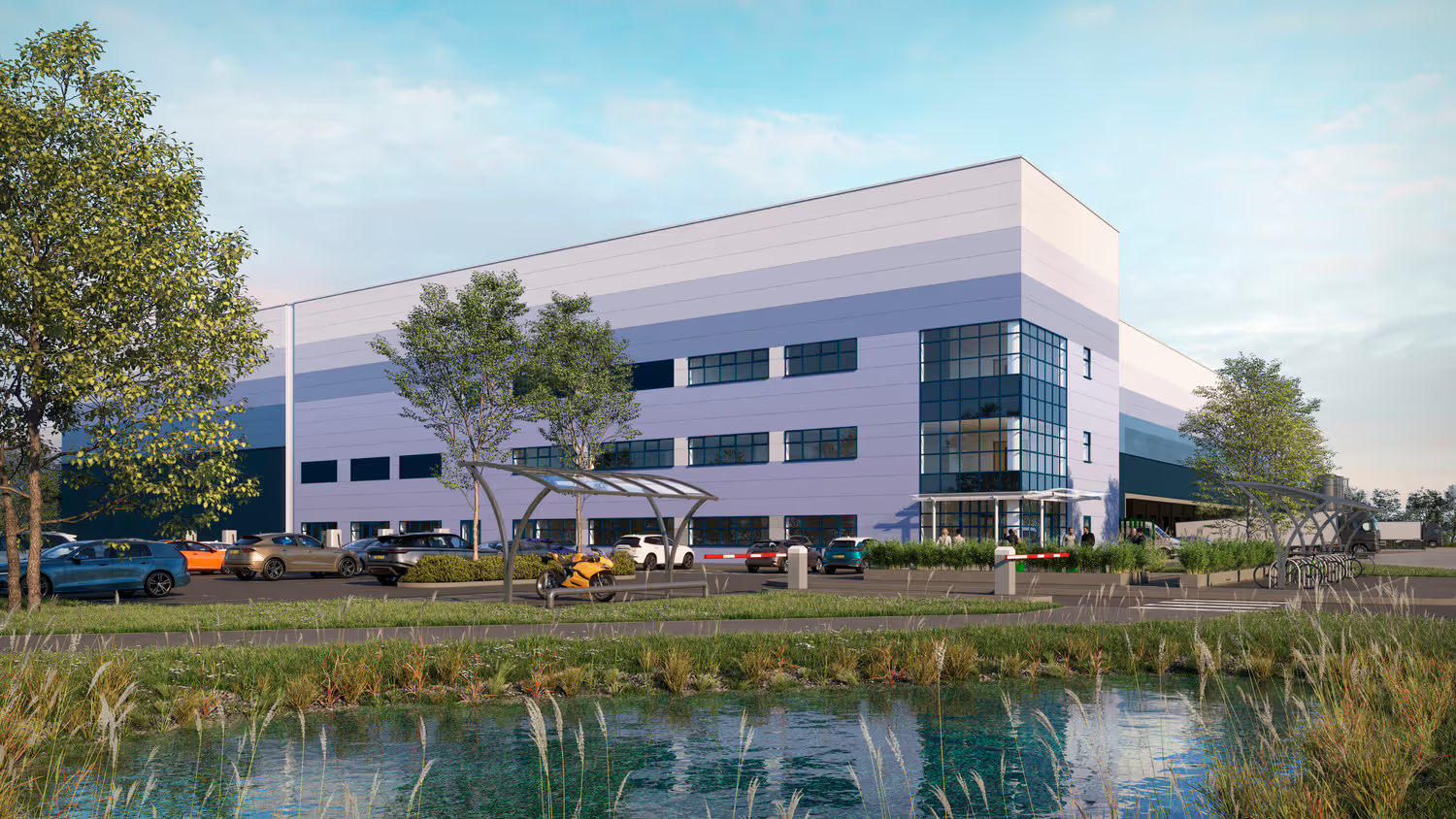
This project demonstrates the awareness among more and more manufacturing companies of the impact they can have when it comes to sustainability by making production processes and buildings more efficient. Solidor was able to bring in new automated processes that were not achievable at their previous locations. The building comprises a large warehouse space at ground level, with offices concentrated over three floors to the front of the building and yards and parking located around the perimeter of the site. The project is targeting BREEAM Excellent and Planet Mark certification with the ambition for the building to achieve up to 15% lower carbon emissions compared with the average UK factory. The design, delivery and efficiency in use of the building has been implemented using BIM to coordinate and produce the works.
Incorporating Wellbeing
The redevelopment of Didcot Quarter repurposed a brownfield site next to the former Didcot Power Station in Oxfordshire into a high-spec industrial complex which puts employee health and wellbeing at its heart.
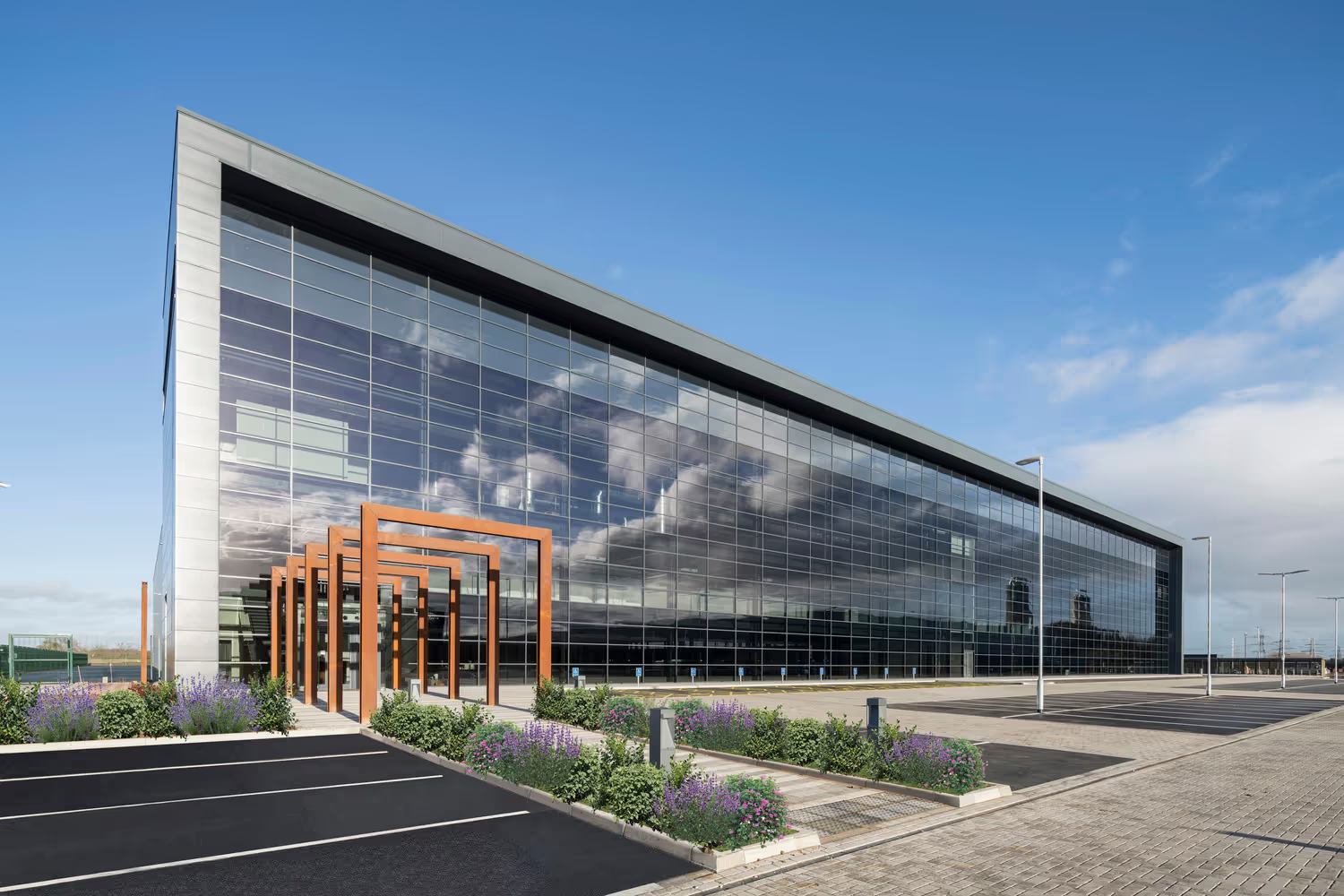
The developers, Savills Investment Management, wanted to apply the high-spec wellbeing and sustainability criteria more typical of a commercial office to a high-tech industrial context, with the use of a wide range of materials, surfaces and finishes such as glass, wood and polished concrete enhancing the building’s positive impact on users and visitors.
A flexible warehouse space utilises natural light through rooflights and transparent areas of wall cladding, whilst absorbing the light from the glazed frontage above and below the office space. In the yard serving the warehouse, the gatehouse is designed to mirror that of the main building with dark grey cladding. Dock levellers and level access doors provide ample facilities for efficient transportation of goods in and out of the warehouse.
Scaled-up manufacturing and distribution
We are currently delivering over 1 million square feet of manufacturing space in the UK.
We are working on an industrial manufacturing and distribution site for TopHat, a company at the forefront of the modular house-building revolution, which is applying robotics and lean manufacturing techniques to increase housing supply, improve quality, reduce costs and protect the environment. At nearly seven times the size of the company’s existing Derby facility, the new 650,000 sqft facility at GLP’s new Magna Park in Corby, Northamptonshire, will be Europe’s largest modular homes plant.
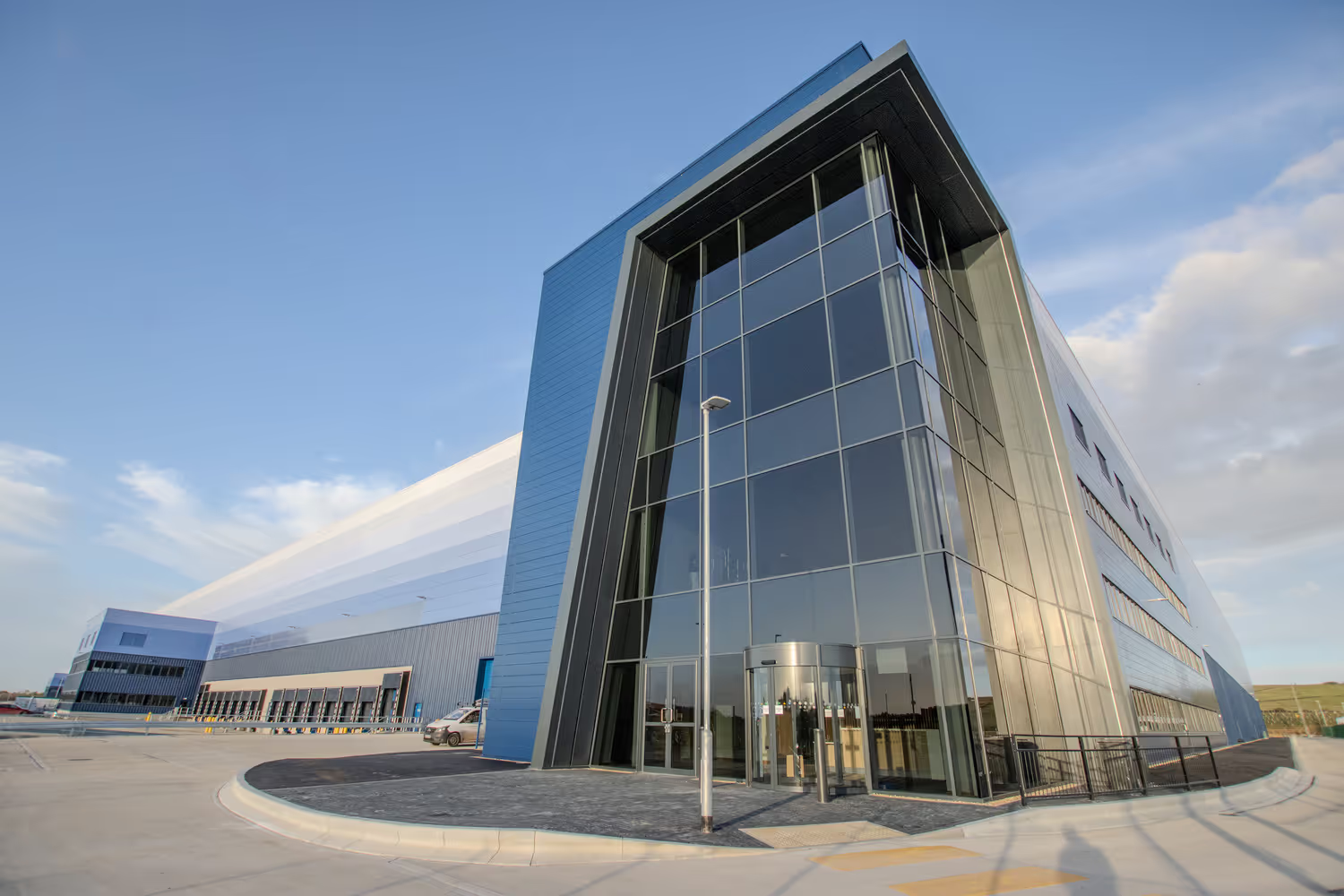
A bespoke cutting-edge design approach incorporates a different grid and bigger doors to ‘normal’, to deliver a state-of-the-art facility that will enable TopHat to bring together on one site the latest robotics, technology and precision engineering techniques – capable of delivering one house every hour – to manufacture and distribute 4,000 new homes per year when it produces its first houses later this year.
Futureproofing
In some cases the developers we work with on pure logistics are seeking the flexibility to mix manufacturing and distribution within a logistics park. To achieve this we can design to base build as logistics with future flexibility to revert from manufacturing to logistics if required by future tenants. In this way developers and their funders can maximise the potential of the site with built in flexibility that future proofs and protects their asset.
Our Research and Development
Our 30-year track record of pioneering work in the design and delivery of world firsts and best-in-class developments in the logistics and industrial sector is inspired by progressive clients who work with us to buck trends and are willing to take risks and push boundaries in the design of their buildings.
Our designs are supported by our award-winning academic research programmes into sustainable design, innovative materials, repurposing and reusing, and applying new data-centric tools and technologies. We are continuously developing processes and tools that allow us to deliver net-zero buildings, and to scientifically measure the impact of their design on the environment and the wellbeing of the people who use them.
We also have three teams of specialists who contribute their specific skills and knowledge. Studio, a group of our most experimental architectural designers, brings imagination and emotion to our designs, Thrive specialises in environmental issues and health and wellbeing, and our Works team champions the digital delivery of projects.
Article tags
Share this insight